How H&M startup Syre is revolutionising polyester recycling
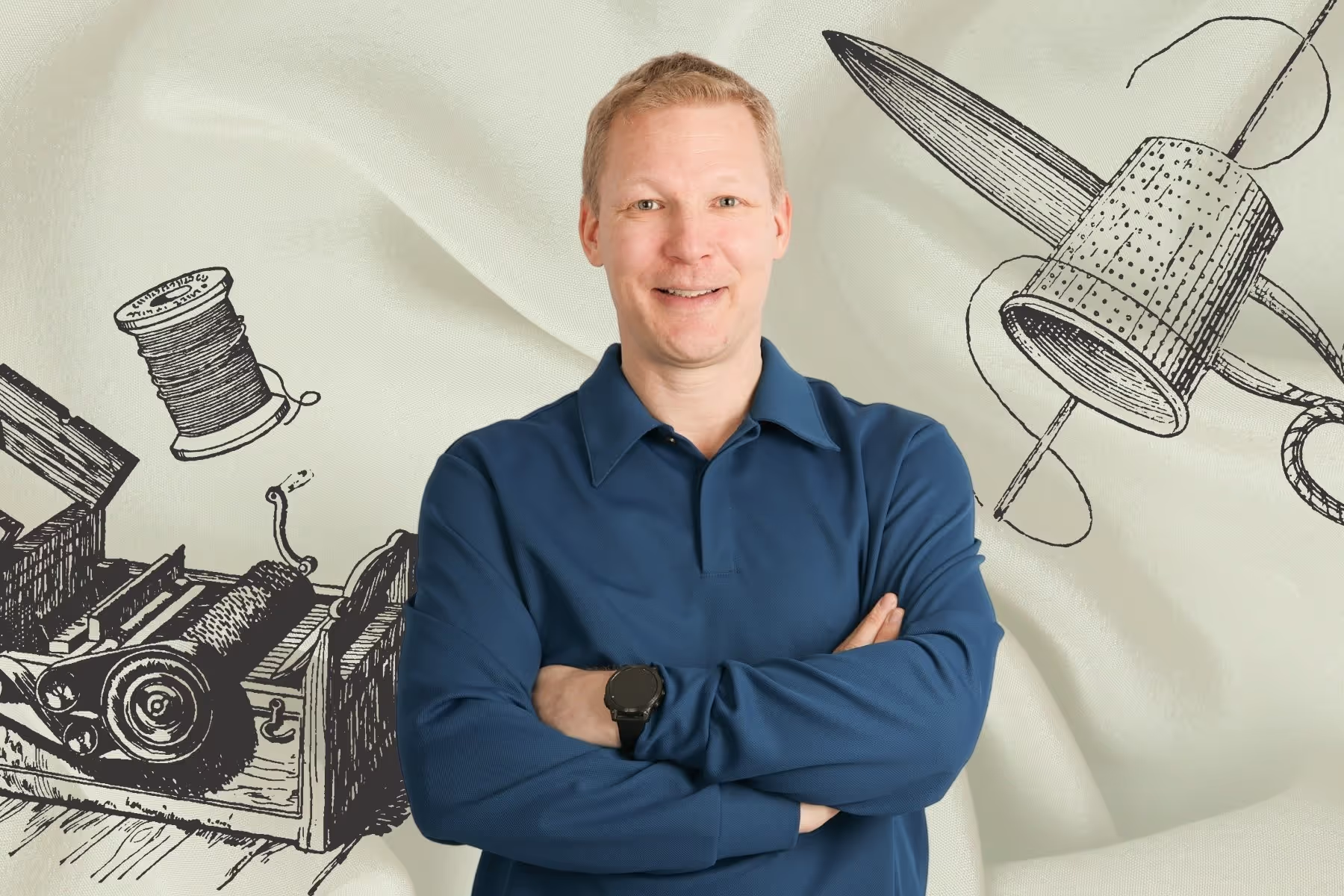
H&M and Swedish impact investment firm Vargas spent years plotting how to recycle polyester on a massive scale.<br><br> The result is textile impact company Syre, which launched in March. In an exclusive interview with Impact Loop, CEO Dennis Nobelius reveals how its building a 'gigascale' operation that could revolutionise textile sustainability.<br><br> Read more:<br> → A step-by-step breakdown of Syre’s innovative recycling method<br> → How Syre raised half a billion kronor from one of the world’s largest climate funds<br> → The tipoff from Northvolt’s Peter Carlsson that brought Dennis Nobelius to Syre
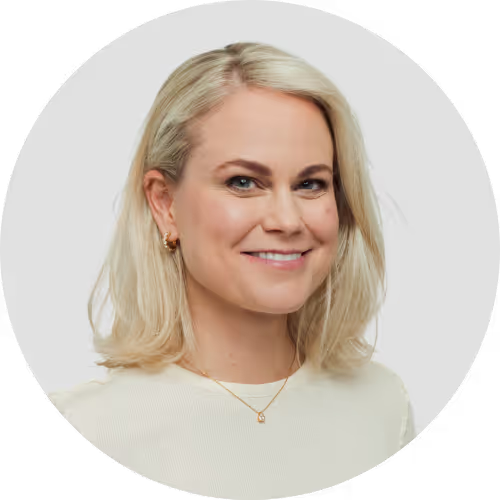
Syre’s CEO Dennis Nobelius proudly holds up a dark blue sweater. At first glance, it looks like any other high street jumper, but this one is made from recycled polyester. What sets it apart? It can be recycled over and over—again and again."
"It's truly circular, unlike many other textiles that can only be recycled once and [end up] with lower quality. This is what we call a 'drop-in product'. It can replace ordinary polyester straight away and you won't notice any difference," says Dennis Nobelius in his strong, song-like Gothenburg dialect.
Syre, which manufactures recycled polyester, has already grabbed mainstream media attention in Sweden. We meet at the startup’s shiny new office in central Stockholm.
With powerhouse backers like H&M and venture capital firm Vargas—fronted by Swedish impact heavyweights Harald Mix, Carl-Erik Lagercrantz, and Susanna Campbell (who’s also co-founder and chair)—it’s no wonder Syre is grabbing headlines. At the helm is Dennis Nobelius, ex-COO of electric car maker Polestar and a Volvo Cars veteran. And the reason he ended up at Syre? That’s down to another big name: Peter Carlsson, founder and CEO of battery maker Northvolt.
"Sanna Campbell had asked him if he knew anyone who would be suitable for the role, and he had recommended me,” says Nobelius. “She invited me for coffee at Vargas' office and said 'I have a job that might suit you'. I didn't apply for it then and there, but the more I understood about the project, I felt it was clearly exciting."
Emma Stjernlöf, former CEO of the sports brand Röhnisch, was also recruited under great secrecy, to the role of Head of Communications and People. She spontaneously joins us for Impact Loop’s interview with Nobelius in one of Syre’s conference rooms.
So, how is this massive project actually going to work—and why is it such an interesting case to watch? Let’s start with the company’s backstory:
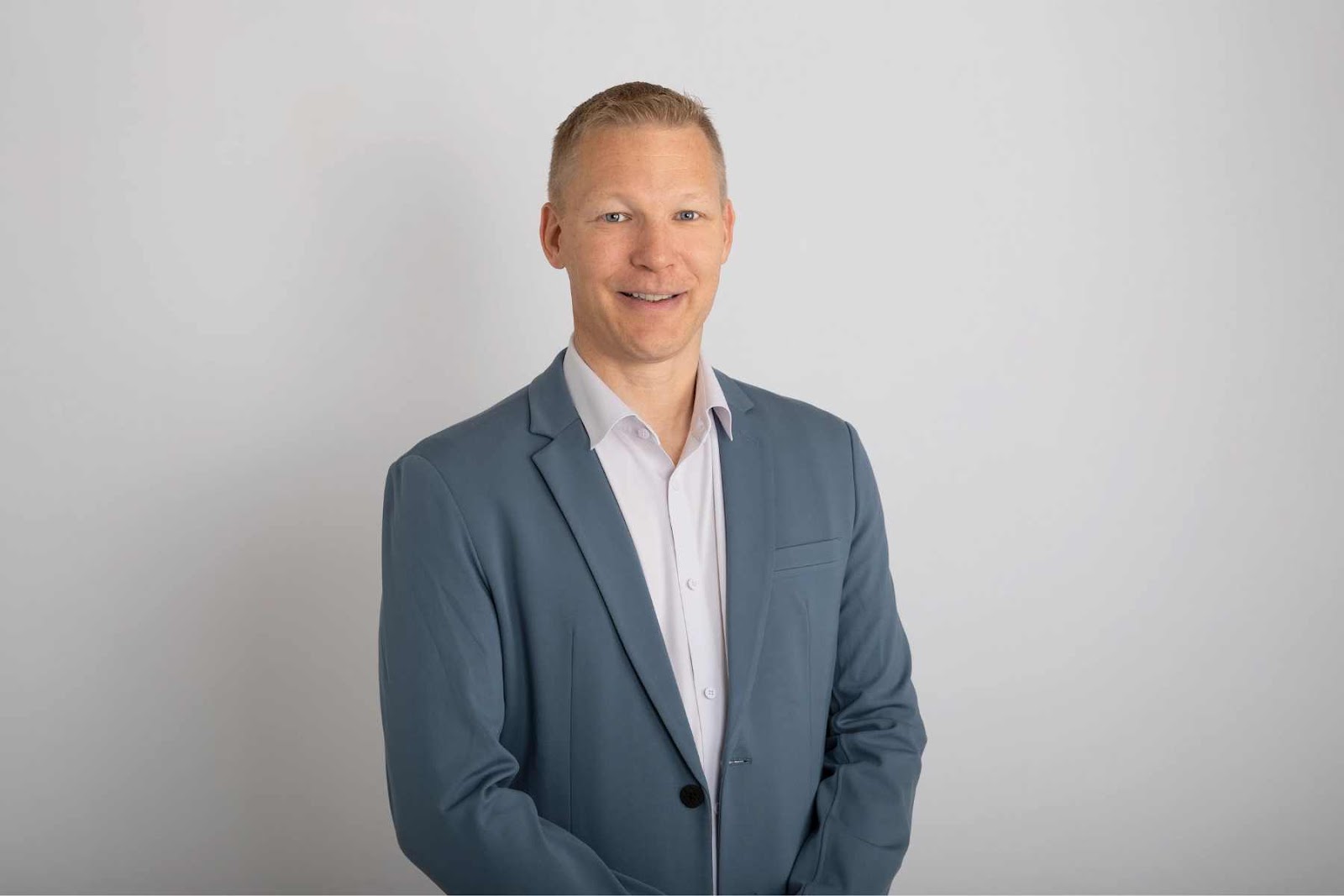
1. The problem: a dirty industry
By now, most people are well aware that the textile industry is a major culprit when it comes to emissions. And the pressure is mounting—with new EU regulations on the horizon, textile producers will soon be forced to take responsibility not just for emissions, but for the waste they create, too.
So, we’re looking at an industry with a major, urgent problem: how can it keep growing while staying sustainable? Can these two goals even be combined? For global retail giants requiring textiles for everything from clothing to cars (like airbags and car seats) and home furnishings (sofas, carpets), using more sustainable materials—especially sustainable polyester—is a key part of the solution.
"Polyester accounts for 54% of the entire fibre market and it's also the fastest growing fibre," explains Emma Stjernlöf.
The problem is that recycling polyester is complex. Various processes and technologies exist, but so far these have been difficult to scale up.
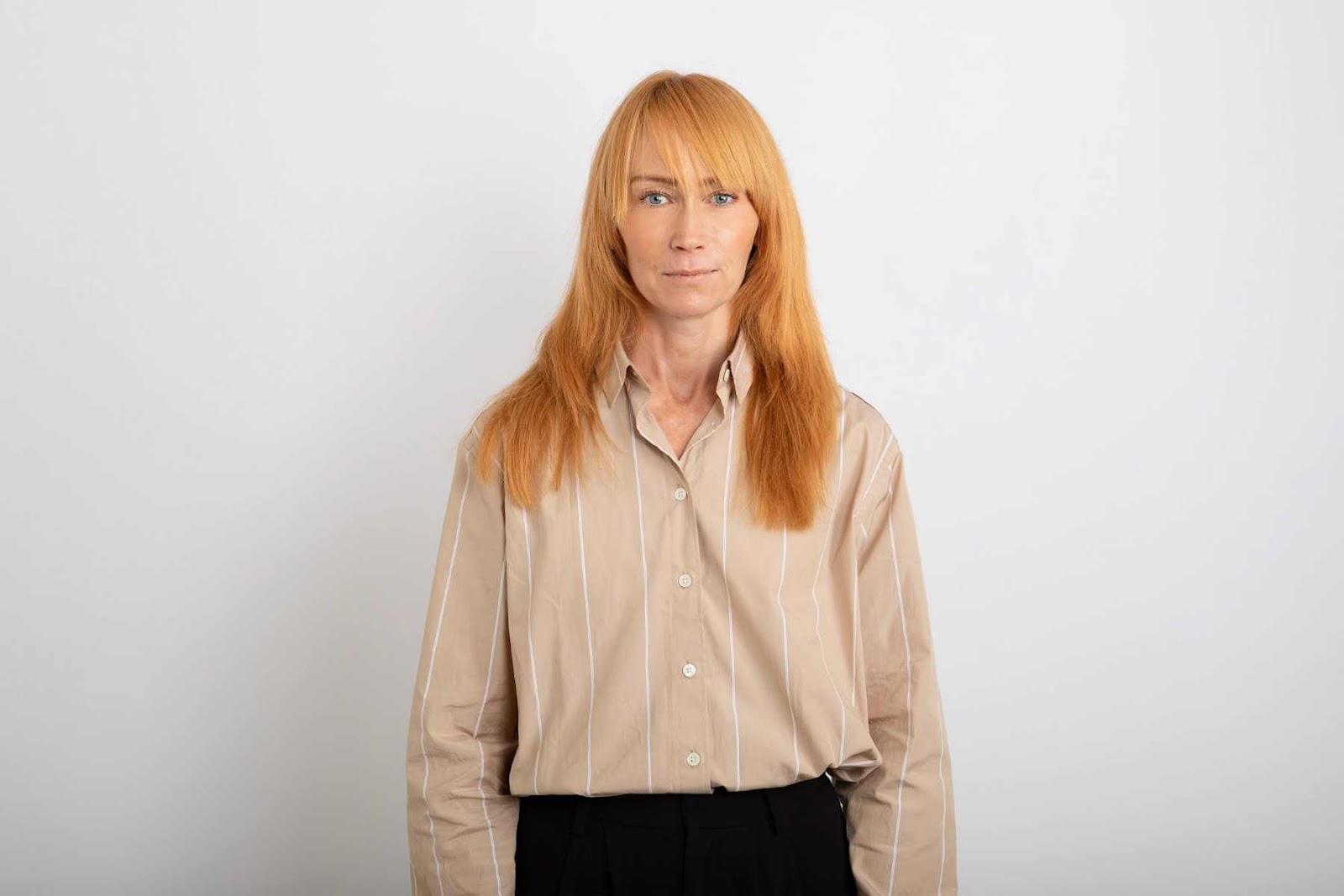
2. A secret acquisition
This is where Syre steps in. For the past two and a half years, Susanna Campbell—Syre's co-founder and a key player in several Vargas companies—and Erik Karlsson, head of investment at H&M, have been exploring different ways to crack the code on circular polyester recycling.
In the end, they landed on a technology developed by two U.S. researchers, who spent over eight years perfecting it. Syre has since acquired the researchers’ company, although Nobelius is keeping the finer details under wraps.
"It's a secret right now," he says.
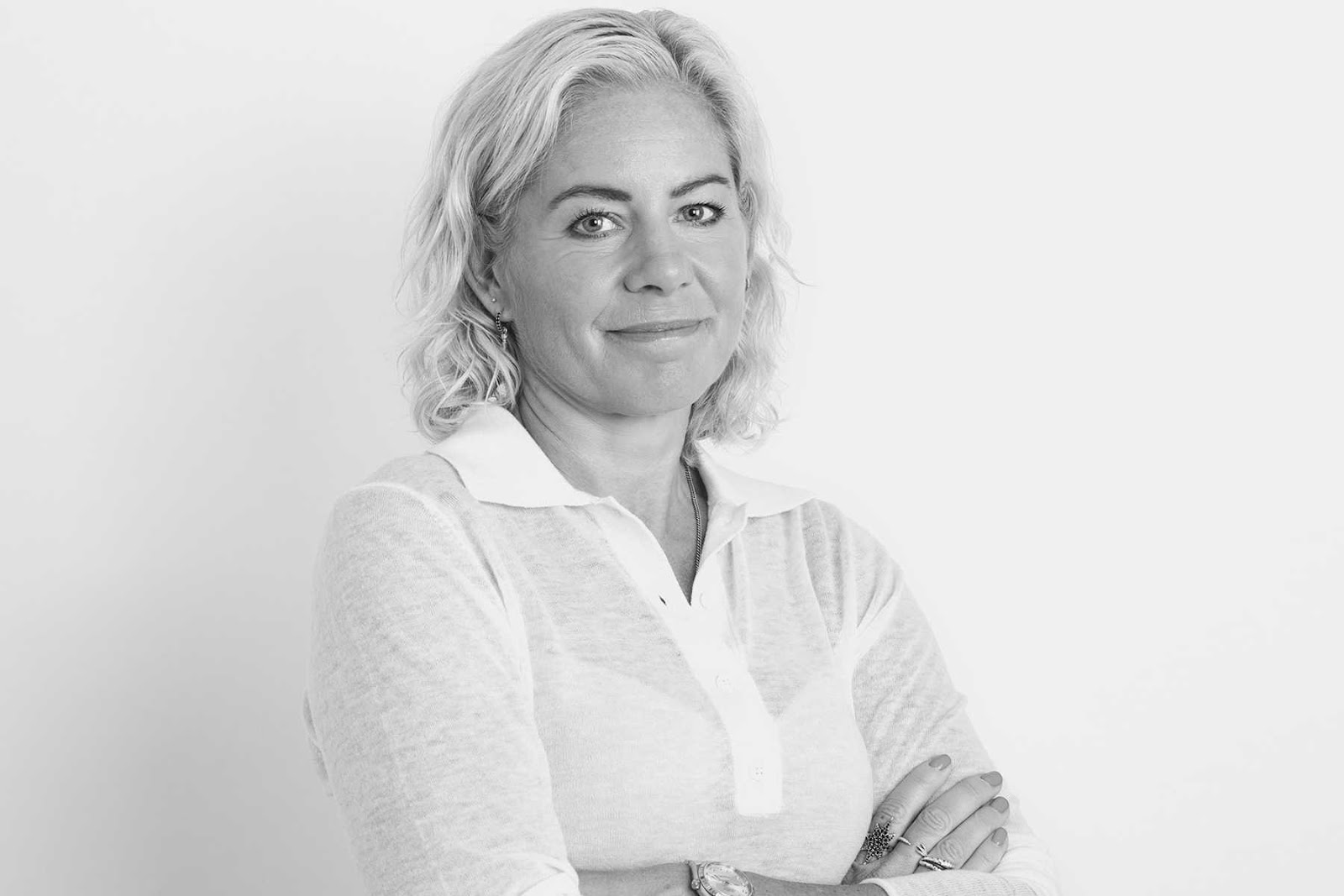
3. The solution: a new toolbox
It could have started and ended there, with a proprietary method for recycling textiles at the facility Syre has now set up in North Carolina, USA. But achieving scalability and profitability means having control over the entire supply chain, from customer to factory.
For Syre, that meant developing their own production process – essentially a toolbox of carefully assembled steps. Outside the conference room where we’re sitting, there’s a row of glass jars, each representing one step in the process.
Dennis Nobelius walks us through them, step by step:
Step 1: Textile collection. Old clothes, airbags, production waste and other items are delivered to Syre's factory in North Carolina. This more challenging than you might think, because there isn’t a historically established system for gathering and managing these kinds of waste efficiently.
Step 2: Textile shredding. A well-established method that mechanically tears textiles apart.
Step 3: Metal extraction. Metal components such as zippers, are ripped out, with the extracted metal sold to traders for a profit. "It's quite a lot actually," says Dennis Nobelius, without giving away the figure.
“H&M realised that there was no existing supplier who could help them achieve their sustainability goals."
4. The USP: a new chemical process
We’ll dive deeper into Step 4, as this is where Syre's innovation really shines. This is the stage that two researchers in the U.S. spent years developing. The process is called depolymerization—a chemical method involving a series of steps that break the material down into a compound known as BHET."
Depolymerization is a critical step in advanced recycling processes, allowing the breakdown of polyester into its base components, such as BHET (bis-hydroxyethyl terephthalate), which can then be repurposed into new polyester, creating a closed-loop recycling system.
"The researchers have tried to make the process as sustainable as possible, without water and by using friendly chemicals," says Nobelius.
He explains that by using this chemical process, the material can be recycled repeatedly. In contrast, if you choose the more common method of making textiles more sustainable by using materials like PET bottles, the resulting fabric is of lower quality and can only be recycled once.
"Brands will move away from that model. If you listen to what the EU has just announced about 'green claims', this [older] method will no longer be allowed to be called sustainable," he says.
Emma Stjernlöf, who also spent 10 years at Adidas before becoming CEO of Röhnisch, adds:
"The sports industry, for example, is a huge user of polyester. They have used polyester made from plastic and called it sustainable. Of course, it's good to take waste and make a product out of it, but it's still 'end of use' for the product. We want to take textile to textile, over and over again," she says.
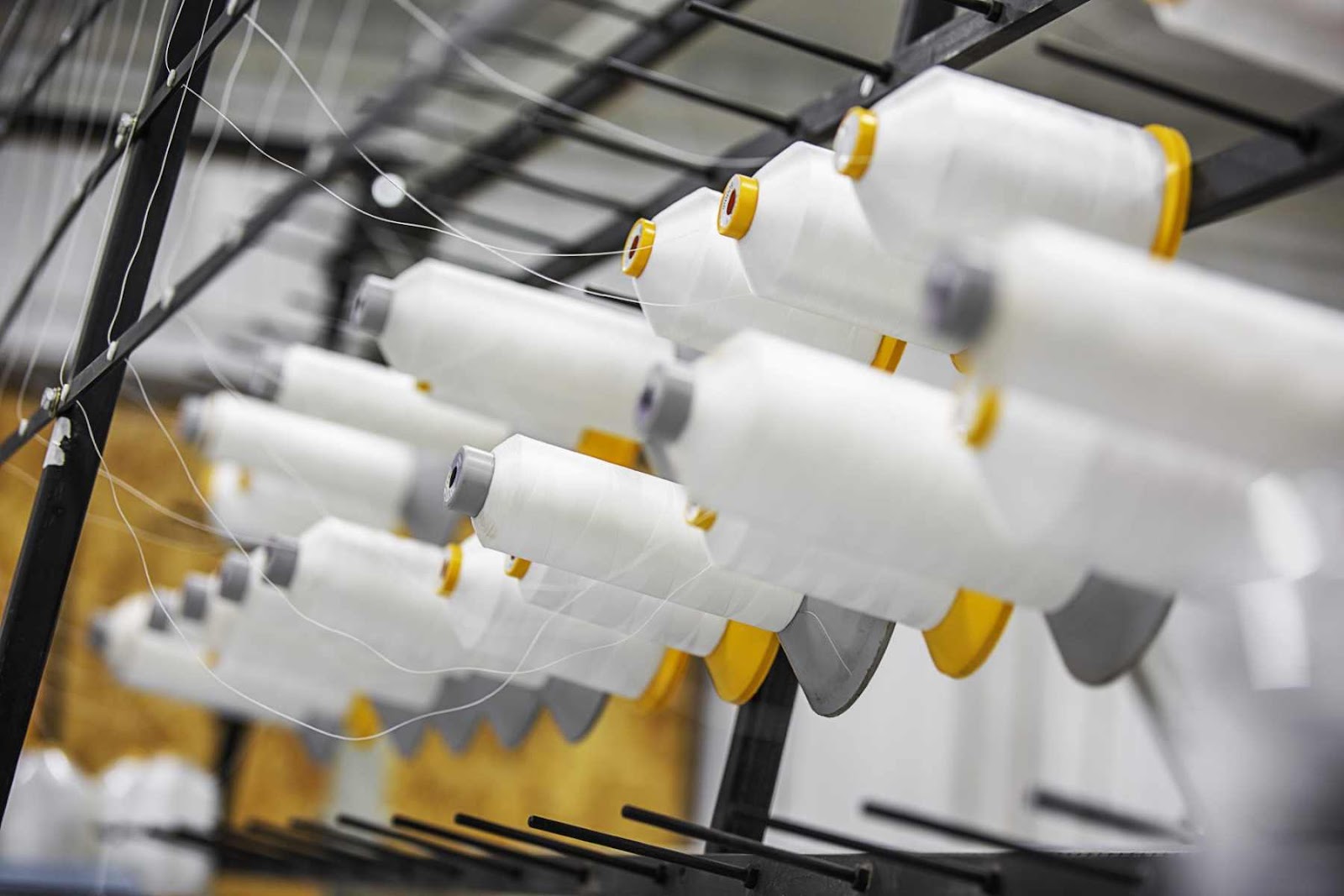
5: The final product – high-value yarn with a green premium
And now, the big finish. Sitting on the shelf in front of us is a large ball of yarn, neatly stored in a glass jar. This isn’t just any yarn, though. This is the endgame—Syre’s high-quality, sustainable polyester yarn, that will soon be heading to the likes of H&M. Byt, the fashion giant is not the only one interested.
"We have lots of customers that we are talking to. They are mainly the big, global giants in everything from clothing to cars and the homeware. That's where we can make the biggest impact," says Nobelius.
The price is pegged to regular polyester, with a markup of a few dozen percent—what’s known as a ‘green premium.’ Dennis Nobelius describes the costs as competitive, according to the simulations the company has run.
In many Vargas-backed businesses, customers are secured early on, and are often co-owners. In the case of Syre, major shareholder H&M has promised orders worth over SEK 6 billion.
"H&M saw that there was no supplier today that could help them reach their sustainability goals. They realised that they needed to make a big change, so they have committed that more than 50% of their future polyester volume will go through us, which is both bold and brave", says Nobelius.
But what is his message to critics who argue that the real solution isn't recycling, but producing fewer textiles?
"It takes both. I know specifically from Daniel [Ervér, H&M's CEO], for example, that increasing the precision of how much you produce is high on his list. We are just one of his three priorities. You need to work on all parts."
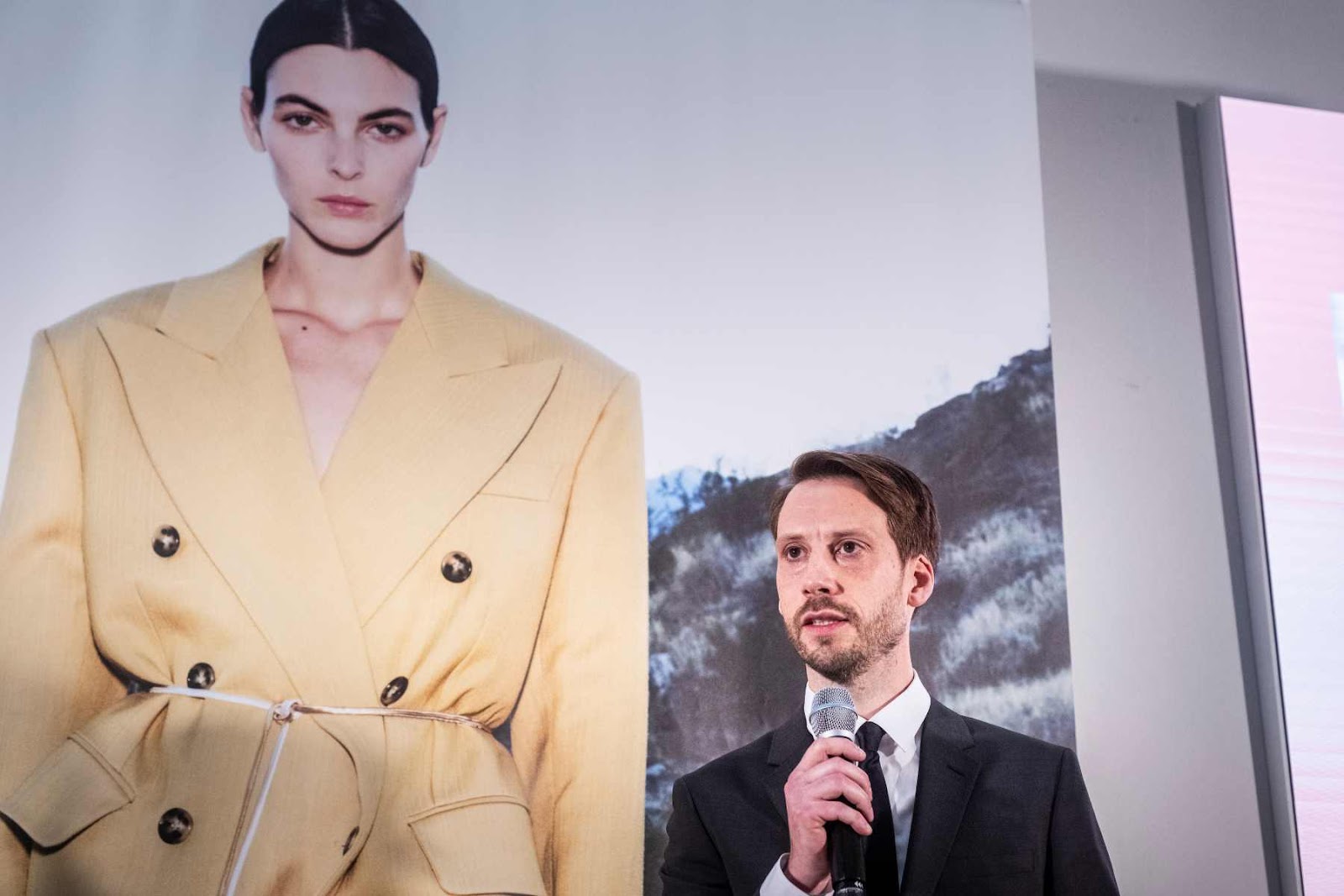
6. Capital: One of the world's largest climate funds
Of course, all of this requires significant funding. Alongside H&M and Vargas, one of the world’s largest climate funds, TPG Rise Climate, has contributed $50 million (around SEK 518 million). They’re also expected to invest further in an upcoming Series B round.
"They are US-based, which is good, and they have a strong connection to Europe. Now we need to find a similar player in Asia," he says.
Syre is focusing on Asia and southern Europe for the location of its larger upcoming factories. A number of criteria have been set, including access to green energy, textile waste, sustainable transportation, and political stability.
When will Syre become profitable?
It’s actually happening quite quickly. But we’ll be reinvesting the profits into the next factory. It’s all about making an impact and reaching the scale needed to truly change the industry."
Translated and edited for Impact Loop Europe by Maddy Savage.
Subscribe to Europe's new platform for impact news
- Quality journalism, interviews, investor profiles and deep-dives
- Join 11 000+ top impact founders and investors across Europe
- Or get our free daily newsletter
Keep reading – get in the loop!
- Håll dig i loopen med vårt dagliga nyhetsbrev (gratis!)
- Full tillgång till daglig kvalitetsjournalistik med allt du behöver veta inom impact
- Affärsnätverk för entreprenörer och investerare med månatliga meetups
Fortsätt läsa – kom in i loopen!
- Håll dig i loopen med vårt dagliga nyhetsbrev (gratis)!
- Full tillgång till daglig kvalitetsjournalistik med allt du behöver veta inom impact
- Affärsnätverk för entreprenörer och investerare med månatliga meetups